Fixing hull battens with two types of West System Expoxy
by Jake Kavanagh 9 May 2019 04:00 PDT
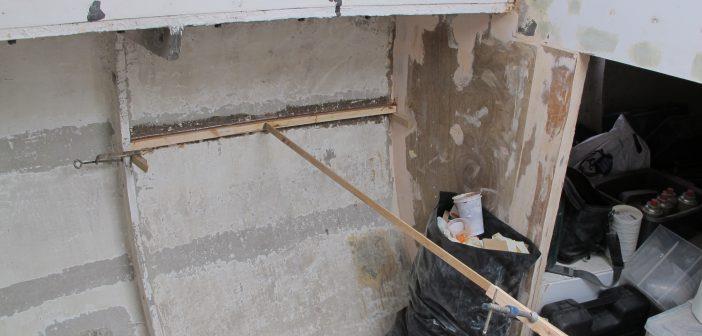
Fixing hull battens with two types of West System Expoxy © Wessex Resins & Adhesives
When fitting out a bare hull or during a refit or renovation project you may find you need to attach some longitudinal or even vertical battens against the bare glass fibre. This is particularly useful for attaching headlining or in this instance insulation to a Ferro-cement hull. To overcome the curve of the hull a strategic dab of WEST SYSTEM G5 Epoxy (sometimes known as five-minute epoxy) will greatly speed up the job of securing the battens whilst the structural epoxy used in the process cures.
On many GRP (polyester) production boats the bulkheads are bonded to the hull with the use of polyester resin and pre-cut strips of Glass Fibre Chopped Strand Mat. This tabbing operation is fairly easy to conduct as the bulkhead is located in place as the glass fibre tabbing cures. Sometimes wooden wedges are used to hold it in place but generally bulkheads are vertically upright and cut to the shape of the hull so there is no need to force it into an angle it doesnt want to stay in.
Our challenge was to fit a series of curved battens that would support about 25mm (1in) of insulation, the idea being that our ferro-cement hull could be given a thermal barrier so it would be comfortable all year round. Many blue water cruisers add extra insulation to their GRP boats if they intend to sail in extremes of climate, hot or cold.
The problem was that at the centre of the curve there is a lot of resistance, as the batten wanted to spring back into a straight line again. We did cheat a bit and buy warped timber from the DIY superstore but we would still have to apply some pressure in the form of a prop to push the batten 25mm out of true against the hull.
The batten would eventually be held by fillets of thickened epoxy but each would need several hours to cure in the low temperatures of an early UK spring. This would mean several props criss-crossing the cabin and we would have to perform an elaborate limbo dance to continue working without dislodging them. However, by tack anchoring the centre of each pine batten with 5-minute epoxy, several could be locked into position in one session, making far better use of time and space.
This is how we attached a series of battens to the inside of our ferro hull. The process is almost identical to a GRP version.
First, we offered a long piece of 25mm x 25mm (1in x 1in) pine between the two frames it would fit between.
We allowed a little extra to compensate for shortening of the batten as it took the curve.
We ran a rough pencil line about 50m (2in) each side of the batten as a guide to prepping the hull to receive later epoxy and reinforcement.
The inside of the hull had originally been painted, so we took the coating off along our guide marks with a coarse (38-grit) sanding disc on a 115mm angle grinder.
A GRP hull is usually covered in some kind of vinyl or carpet lining, which can leave contact adhesive behind. This all needs cleaning off. A wire brush on a grinder works well and is the weapon of choice for specialists who reline hulls.
A wipe down with acetone, or better still WEST SYSTEM 850 Cleaning Solvent, will remove any contaminants from the surface of the polyester for a better bond.
We marked the area in the centre of the batten where we would be tacking it to the hull. This area would be left clean of any other resins.
Pre-warmed in our hot box, a mix of WEST SYSTEM 105 Epoxy Resin and 205 Fast Hardener was brushed onto the hull and also onto the batten, paying particular care to coat the end grain of the wood. This is where moisture can begin its track inwards.
We also left a dry area right in the centre of the batten and an opposing dry spot against the hull. This is where the G5 epoxy would be bonding.
Props comprised of two sections of wood held in the centre by a couple of G-clamps were offered up for the correct length to compress the 25mm square batten hard against the hull.
We then mixed up a small amount of G5 epoxy, measuring the two components out accurately by eye to create a 1:1 mix by volume. This is fairly easy to do as the resin and hardener are of similar consistency.
We put a dab of this mix behind the centre part of the batten and then compressed the batten with the prop. A hammer can be used to gently tap the batten up or down to get the correct alignment inside the hull. Although the G5 epoxy sets in literally five minutes at 20°C, this cure window is slightly longer in the chill of a March day.
With the position confirmed, we then made a small fillet using the G5 epoxy. It can be thickened using 406 Colloidal Silica Filler but we found it was thick enough as it was. This fillet was left to harden as we went to work on cutting and assembling the next batten.
A few minutes later, a thumbnail test showed us that the G5 epoxy was rock hard. This allowed us to remove the prop and use it on the next batten. The G5 epoxy was behaving as a rapid cure adhesive clamp, allowing us to keep the cabin uncluttered. As we had mixed plenty of WEST SYSTEM 105/205 epoxy we added some 406 Colloidal Silica Filler and then took our time to make an even fillet on each side of the batten. (The brown-coloured 407 Filleting Blend is a better choice but we had run out. The 406 filler was handy and a good replacement.)
The fillets will have ample strength by themselves but boat owners used to working with GRP would probably want to add an extra layer of glass fibre reinforcement over the top. The edges of the batten need to be rounded first, as seen in the diagram, and the extra reinforcement will certainly add to the overall strength of the hull and make it less likely to flex.
This last batten completed the set on the starboard side ready to receive the silver-backed foam insulation. This will reflect outside heat back out and inside heat back in.
A final touch was to open up a slot in the centre of the batten and line the sides with epoxy. This will allow any condensation to find its way into the bilge, with the grain of the pine protected against fresh water rot. In hindsight, this slot could have been pre-cut and would have made the batten easier to flex.
See more stories and tips at epoxycraft.com/category/blog