UMaine Composites Center receives three Guinness World Records related to largest 3D printer
by Meghan Collins/UMaine Composites Center 13 Oct 2019 04:23 PDT
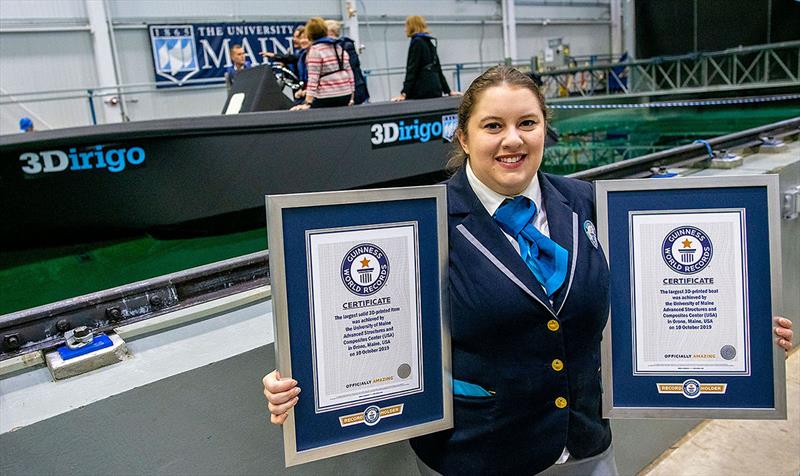
Guinness World Records © Meghan Collins
More than 250 federal and state officials, business executives, University of Maine System leaders and community members were on hand to witness the UMaine Advanced Structures and Composites Center receive three Guinness World Records on Oct. 10 for the world's largest prototype polymer 3D printer, largest solid 3D-printed object, and largest 3D-printed boat.
The event culminated with the world's largest 25-foot, 5,000-pound 3D-printed boat, named 3Dirigo, being tested in the Alfond W2 Ocean Engineering Laboratory, an offshore model testing facility equipped with a high-performance wind machine over a multidirectional wave basin. The ceremony was a milestone in UMaine's leadership in cutting-edge composite material research and development, and commitment to use Maine's vast natural resources to drive innovation that generates major economic development opportunities in the state and beyond.
"I was delighted to join UMaine's celebration unveiling the world's largest 3D printer and largest 3D-printed object," said Sen. Susan Collins. "The future of the [UMaine] Composites Center is bright, thanks to the excellent working relationship between UMaine, Oak Ridge National Laboratory and many other federal agencies, which will support next-generation, large-scale additive manufacturing with biobased thermoplastics. As a senior member of the Senate Appropriations Committee, I helped secure $20 million for this exciting collaboration, and an additional $20 million is included in the committee-approved energy funding bill. By working together, UMaine and Oak Ridge will strengthen environmentally responsible advanced manufacturing throughout America, as well as the forest-products industry in Maine."
"Maine is the most forested state in the nation, and now we have a 3D printer big enough to make use of this bountiful resource," said Sen. Angus King. "Today marks the latest innovative investment in Maine's forest economy, which will serve to increase sustainability, advance the future of biobased manufacturing and diversify our forest products industry. This is a huge opportunity for the state of Maine, and I'm grateful to everyone — especially the University of Maine and the FOR/Maine initiative — for their work to make this day a reality."
"As we saw today, the University of Maine Composites Center does award-winning, cutting-edge research that makes Maine proud and will bring jobs to our state," said U.S. Rep. Jared Golden. "Their work, like the boat and 3D printer we're here to see, has impressive potential to change how we make things out of all sorts of materials — including Maine wood fiber. Today is about three Guinness World Records, but it's also about celebrating innovation that will help protect and create good-paying Maine jobs in forest products and manufacturing."
The new 3D printer is designed to print objects as long as 100 feet by 22 feet wide by 10 feet high, and can print at 500 pounds per hour. The one-of-a-kind printer will support several ambitious initiatives, including development of biobased feedstocks using cellulose derived from wood resources, and rapid prototyping of civilian, defense and infrastructure applications.
A $20 million research collaboration with Oak Ridge National Laboratory (ORNL), the U.S. Department of Energy's largest science and energy laboratory, will support fundamental research in key technical areas in large-scale, biobased additive manufacturing. The partnership between UMaine and ORNL will advance efforts to produce new biobased materials conducive to 3D printing of large, structurally demanding systems. The research will focus on cellulose nanofiber (CNF) production, drying, functionalization and compounding with thermoplastics, building on UMaine's leadership in CNF technology and extrusion research. By placing CNF from wood into thermoplastics, bioderived recyclable material systems can be developed with properties that may rival traditional materials, possibly even metals.
"This is an exciting achievement in our partnership with the University of Maine," said Moe Khaleel, associate laboratory director for Energy and Environmental Sciences at ORNL. "This new equipment will accelerate application and integration of our fundamental materials science, plant genomics and manufacturing research to the development of new sustainable bioderived composites, creating economic opportunity for Maine's forest products industry and the nation."
Biobased feedstocks are recyclable and economical, providing competitive advantages for Maine's manufacturing industries, including boatbuilding. The UMaine Composites Center received $500,000 from the Maine Technology Institute (MTI) to form a technology cluster to help Maine boatbuilders explore how large-scale 3D printing using economical, wood-filled plastics can provide the industry with a competitive advantage.
The cluster brings together the expertise of UMaine researchers and marine industry leaders to further develop and commercialize 3D printing to benefit boatbuilders in the state. By 3D printing plastics with 50% wood, boat molds and parts can be produced much faster and are more economical than today's traditional methods.
"With this remarkable feat, the University of Maine continues to demonstrate that it's a worldwide leader in catalyzing innovation, advancing new technologies and driving economic growth for our state," said Gov. Janet Mills. "On behalf of the people of Maine, I congratulate the university on this historic accomplishment."
To demonstrate the new printer's capabilities, UMaine 3D printed a 25-foot patrol boat with a hull form developed by Navatek, a leader in ship design and a UMaine Composites Center industrial partner. The 5,000-pound boat was printed in 72 hours — from Thursday, Sept. 19 to Sunday, Sept. 22. The massive printer, with both additive and precise subtractive manufacturing capabilities, enables rapid prototyping for both defense and civilian applications.
UMaine also showcased a 3D-printed, 12-foot-long U.S. Army communications shelter. The new printer will support programs with the U.S. Army Combat Capabilities Development Command (CCDC) Soldier Center and its mission to develop rapidly deployable shelter systems for soldiers. Other use areas include concealment applications, structural shelters and high-temperature fire retardant materials for vehicle-mounted shelters.
"The innovation that we have witnessed here at the University of Maine will revolutionize how the Army prototypes and manufactures shelters, vehicles and other large systems," said Col. Frank Moore, military deputy for the CCDC Soldier Center. "The lighter yet stronger 3D printed systems will advance the state of the art in additive manufacturing, forging the future of expeditionary equipment IAW with the Army's new policy on advanced manufacturing."
Working with the U.S. Army Corps of Engineers, the 3D printer will further advance UMaine's groundbreaking innovations in rapidly deployable, low-logistics infrastructure systems. That includes a 5,000-pound, 21-foot-long 3D-printed mold for a new 76-foot-long composites bridge girder. The girder has been licensed to a UMaine spinoff company, Advanced Infrastructure Technology, that is in the process of fabricating girders for a bridge to be constructed in Hampden, Maine in summer 2020. In addition, rapid production of stay-in-place concrete formwork is a potential solution for both infrastructure and coastal resiliency construction applications.
"The U.S. Army Corps of Engineers Engineer Research and Development Center (ERDC) is proud of the accomplishments achieved in the long-standing collaboration with University of Maine in military engineering," said David Horner, director of the ERDC Information Technology Laboratory. "The large 3D printer capability will greatly support research in applications to both military engineering and national civil works infrastructure. This unique facility, along with applications of high-performance computing, will help advance the rapid-prototyping and additive manufacturing capability of DoD."
Bartley Durst, director of the Geotechnical and Structural Laboratory at ERDC, noted "this capability to produce large, biobased prototypes through advanced high throughput additive manufacturing capabilities will provide critical technology development of solutions in force projection and force protection for our nation's war fighters."
"We foresee that this capability will foster the development of on-demand force projection nodes, logistics over the shore solutions, as well as capabilities for response and recovery to natural disasters, globally," Durst said. "Additionally, this large 3D printing capability supports the development of rapid construction of transportation infrastructure emplacement, repair and rehabilitation for this critical need of our nation. The USACE ERDC looks forward to the continued, productive collaborative partnership with the UMaine."
"We are truly honored to be working with leaders from the Maine boatbuilding industry, Maine Forest Products Industry, the national construction industry, Maine Technology Institute, Oak Ridge National Laboratory, the U.S. Dept of Energy Advanced Manufacturing Office, the U.S. Office of Naval Research, the U.S. Army, and the U.S. Army Corps of Engineers," said Habib Dagher, executive director of UMaine's Advanced Structures and Composites Center. "With this large printer, we will be able to accelerate innovation and prototype development in both the civilian and military sectors.
"This 3D printer is an outgrowth of research we have been doing for 15 years in combining cellulosic nano and micro fibers with thermoplastic materials," Dagher said. "Our goal is to print with 50% wood products at 500 pounds per hour, and achieve properties similar to aluminum. We thank our congressional delegation for their support."
Attending the Oct. 10 ceremony were U.S. Sens. Susan Collins and Angus King, U.S. Rep. Jared Golden, officials from the Maine Governor's Office, and leaders at the U.S. Army Combat Capabilities Development Command Soldier Center, U.S. Army Corps of Engineers, U.S. Department of Energy Advanced Manufacturing Office, Oak Ridge National Laboratory, the University of Maine and University of Maine System.
Earlier this year, Collins and King joined leaders from the U.S. Department of Energy, UMaine, and Oak Ridge National Lab in Washington, D.C., to announce the launch of the $20 million large-scale biobased additive manufacturing program that will use the 3D printer. The work of the Economic Development Assessment Team (EDAT), created by Collins and King in 2016 to create strategies for job growth and economic development in Maine's forest economy, led directly to the partnership between UMaine and ORNL.