Genny up to power up
by Lyman-Morse Boatbuilding 1 Feb 2020 10:54 PST
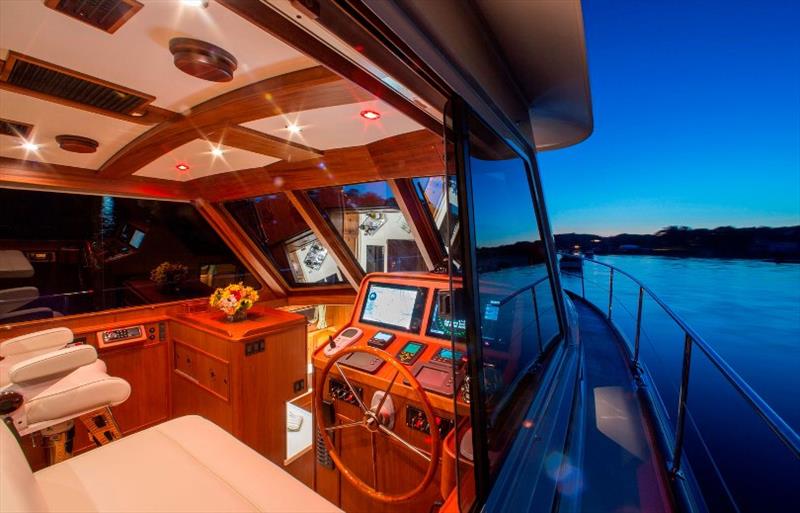
Interiors onboard Peregrine, a 42' flybridge twin jet designed by C. Raymond Hunt © Lyman-Morse Boatbuilding
Boats used to be so simple. The engine powered the boat. Its pistons turned the propeller. Its alternator charged the batteries and ran the radio, running lights, and some low-key interior lighting. The engine warmed water, albeit to tepidness.
No more. Today's vessels are worlds unto themselves chock full of lights, electronics, entertainment features, gyroscopic motion control, retractable awnings, and sophisticated climate control systems. All need power — and a powerful marine generator — to keep them running at a swipe of a finger. Estimates say that marine generators see three to five times more use than a vessel's core propulsion engine.
Demand for sophisticated marine powerplants is among the most common requests at Lyman-Morse. New builds like the Lyman-Morse Hood 57, Anna, and Peregrine featured sophisticated generation, as did refits like Red Sky and Scout.
Tailoring modern marine generators to a particular boat has evolved into a complex team sport between power engineers, project managers, and installers. "It all comes down to taking the time to walk through a proper install," says Chaz Guthrie, mechanical supervisor at Lyman-Morse, who's been involved in generator installations for the past five years.
"To get there, we start with a good engineering plan and process. Then it's just about getting the details right."
How big is big enough?
The devil-in-the-details for a proper generator installation starts with listing the power demands of all the appliances, navigation aids, and climate control systems on a boat. Genset makers like Cummins offer excellent online load calculation resources. But such tools often fail to factor in the dynamic loads of which devices are running at a given time. So, it falls to Lyman-Morse's project managers to work with boat captains and/or owners to accurately predict a vessel's true power demands.
Allowances must be made for the ten- to twenty-fold spike in power demand that can be caused by the so-called in-rush current that surges through an electric motor as it starts. Such spike loads can be mitigated by so-called soft start technologies. Regardless, spike loads should never strain generators, which should never run at less than 25 percent, or more than 80 percent, of total capacity.
To break in generators for proper services, Lyman-Morse's power systems engineers, including Toby Teele, are careful to run new generators at manageable loads for roughly 50 hours to break them in. Smaller units, usually measured in electrical kilowatts, or eKW, save fuel and weight. So Teele often supplements generator energy needs with inverters. He is also testing emerging auxiliary power system like Intregral that siphon and store power from a boat's propulsion engines. Power can also be cached in a new family of carbon foam or lithium-ion batteries. Sophisticated Process Logic Controllers (PLCs) can also be installed to turn off systems, shed load, and protect generators.
Installing a good Genny
Next is positioning the generator, ventilation, and exhaust. Usually, generators share enclosures with propulsion engines. Engine rooms must be well-ventilated, close to fuel supplies and electrical networks. They must meet an ever-expanding roster of emission regulations. Ventilation must be optimized for the size of the engine, its operating speeds, and the volumetric efficiency of the air-fuel mixture entering the engine block.
Raw cooling water must pass properly into through-hulls. Exhaust lines are often fitted with anti-siphon devices. Fuel lines must be properly sized, filtered, and installed to meet standards. Fuel temperature must be kept low enough to combust properly and maintain generator efficiency. Below-surface exhaust systems must also be carefully engineered to prevent flooding: A half-inch rise per foot of exhaust line is required, with a minimum step-up of 12 inches between the engine exhaust elbow and the water muffler.
Electrical installation is also a key. All connectors must be properly shielded and grounded. Motion is a fact of life under way; a poorly insulated electrical connection can abrade and cause a fire.
Mounts also matter. A rock-solid generator mounting tray must be securely bolted to a sound shield pan, that is in turn soft-mounted to hull structures beefy enough to prevent generators from rocking in rough seas. Larger systems require up to a three-inch clearance. A generator can never touch a pipe or wall fitting, or it can make a terrible racket, or do terrible damage. All this and more must be done to the highest possible standards.
Ironically, Guthrie says that the key to the most complex power-generation setup is keeping the installation simple. "It all comes down to doing a simple installation," he says. "When the plan is right, it's easy to follow the specifications. The systems just fit together, and you just know it's going to work."