Production of the new Back Cove 372 is underway!
by Back Cove 16 May 2021 08:37 PDT
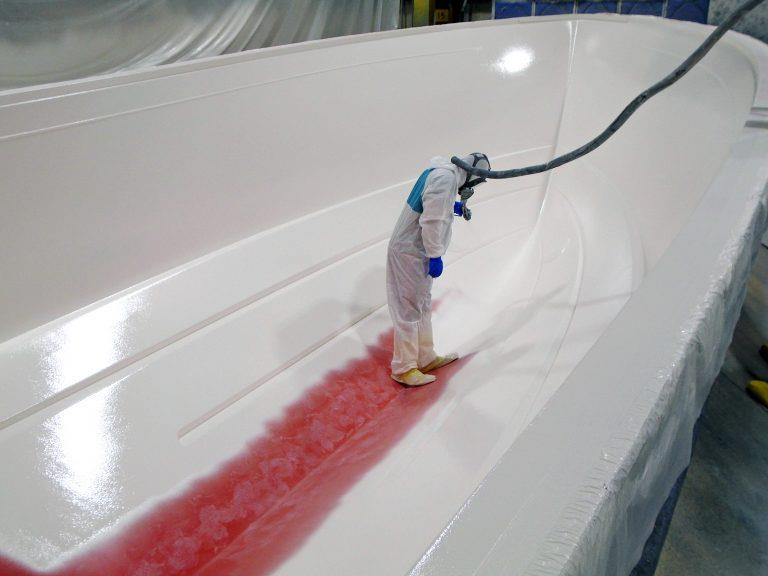
Back Cove 372 © Back Cove Yachts
Production has begun on the prototype hull of the newly redesigned Back Cove 372, and we can't wait for the finished result. We are pleased to announce that the first hull has been successfully pulled from the mold (stay tuned for regular production updates as the build progresses). Long-time readers will be very familiar with the process depicted below, but we'll run down the steps for our new readers!
First, the hull mold is prepared (cleaned and waxed) to ensure a smooth and easy release. The more the mold is used and worn the more difficult it becomes to release a part, which is why the Back Cove 37/372 hull mold was re-tooled (a new mold made with the exact same geometry as the original) several years ago. When the mold is prepped and ready, the fun part begins. During the "layup" stage the dry components of the hull are stacked one atop the other from the outside in, meaning the first thing to go into the mold is the gelcoat.
Following the gelcoat is a layer of "chop" - short strands of fiberglass that both protect the gelcoat during the layup process and help to ensure a fair finish on the completed hull. Next, sheets of fiberglass are laid into the mold so the weave of each layer runs perpendicular to the weave of the layer before, ensuring optimal strength throughout the hull. These layers are temporarily tacked into place with adhesive spray to prevent any shifting or movement.
Back Cove Yachts also dry-installs our hull stringers, a practice that is not always possible for other manufacturers (including our sister company, Sabre Yachts) due to the size and/or weight of their hulls. By infusing the stringers with the rest of the hull, Back Cove creates astoundingly strong hulls that are also remarkably light.
With all the dry materials in place, the layup stage is complete and it's time for infusion!
The hull is carefully bagged and an air-tight seal is created around the entire part. A vacuum is used to create a negative pressure system within the mold which draws resin through the part using a complex series of tubing and valves. This process ensures that the resin is evenly distributed preventing dry spots and over-saturation. After the vacuum process, the Lamination department carefully monitors the temperature to ensure it cures perfectly.
Finally, it's time for the big reveal! When the hull is fully cured the Back Cove production team uses a series of chains and winches to lift the completed hull from the mold, revealing a beautifully fair surface and pristine gelcoat.
The finished hull is lowered into a cradle and transported to the next phase of the production process! We hope you'll continue to follow along with us, as there's truly nothing quite like watching a prototype hull make the transition from idea to finished product. Our team of craftspeople is second to none, and they give every ounce of their enthusiasm and skill to their work, whether they're building the first hull of a brand new model, or wrapping up the 1000th Back Cove.
The Back Cove 372 is expected to splash late this summer and make her boat show debut at the United States Powerboat Show (Annapolis, Maryland) in October 2021.