Bering Exclusive: Made of Steel - Materials in yacht building
by Bering Yachts 3 Mar 2023 02:23 PST
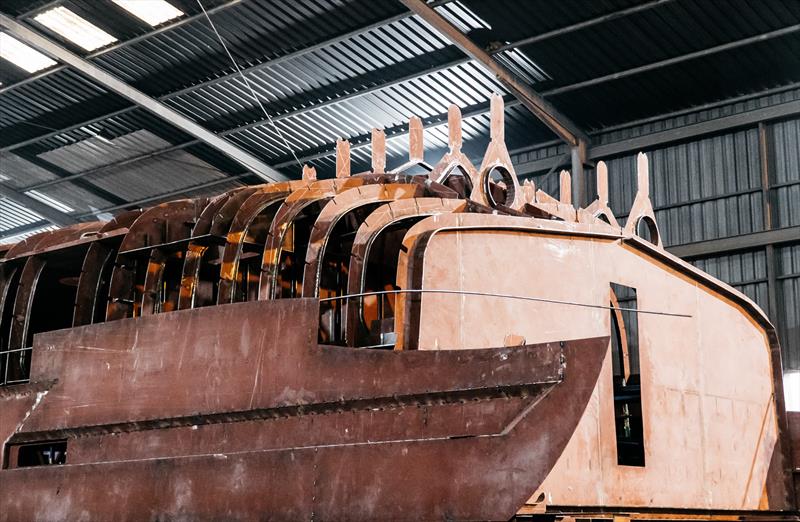
Steel shipbuilding © Bering Yachts
Some of the first vessels with true metal hulls as we know them today were built at the end of the 18th century. Prior to that time, metal was incorporated as a component of marine construction.
For instance, lead and copper plates were used since ancient times to protect the wooden hulls. Then, beginning to the mid-19th century, the mass production of steel boats began in earnest.
Steel's wider availability as well as its sturdiness, resistance to environment, and many other advantages over wood eventually made it the most-used material in military and commercial shipbuilding. These older steel boats were safe and reliable, but heavier steel travels more slowly, or requires more resources to increase speed. That's why lighter materials, such as aluminum and fiberglass, came into play. Regardless, these lighter materials cannot match steel's strength and performance. This is why steel still remains the material of choice for the most commercial vessels, which account for a large portion of all the world's tonnage and cargo-carrying capacity.
Steel shipbuilding in numbers:
- The global shipbuilding market was valued at $142.52 billion in 2020, and is projected to reach $195.48 billion by 2030 (Valuates Reports, 2022).
- In 2018, the global ship plate market size was estimated at over $33 billion (ship plate is a hot rolled steel sheet that is used to construct the hull of a ship). (Global Market Insights, 2019)
- Roughly 5% of all world steel production goes into shipbuilding (World Steel Association, 2019)
- The world's largest steel ship is Prelude FLNG (1,601 feet long, 243 feet wide, GT 300,000 tons, with more than 200,000 tons of steel used in the build).
As referenced previously, both aluminum and fiberglass boats are also utilized in naval construction. These materials are still durable and are lighter than steel, which is why they are commonly used for modern recreational shipbuilding. Nowadays companies who are looking to build safe and stable boats need to decide which materials - steel, aluminum, or fiberglass - best suit their vision of quality and reliable seagoing. To make the correct choice, one needs to look deeper into materials' qualities and features.
For example, material choice defines a boat's weight. A heavier boat has higher displacement; it can carry more and has better seaworthiness. On the other end of the spectrum, a lighter boat can potentially enhance speed and mobility. So, your material of choice will define which type of naval architecture you will implement, what kind of boats you will be making, and which tasks these vessels will be capable of handling. Naturally, different tasks call for different materials.
So why does Bering pick steel for its boats?
Of course each material choice has its benefits and drawbacks. Steel is durable but heavy. Aluminum is resistant to corrosion, but too light for most applications. Fiberglass has plasticity, which makes it easier to mold to shape, but is brittle. Finding the right material for a task means discovering balance.
Steel
Steel is an alloy made up of iron with addition of carbon to improve its strength. However, an excessive amount of carbon makes steel brittle in low temperatures and deteriorates its weldability. Therefore, the carbon content must be carefully monitored. Other alloying elements are added to steel in order to create metal with specific characteristics needed for different tasks. The steel used in marine construction has to be strong and resistant to extreme temperatures and the elements. For example, the highest strength AH-36 marine grade steel - in addition to carbon (less than 0.2%) - is enriched with manganese (less than 1.3%), silicone (less than 0.3%), aluminum (less than 0.02%), and other elements. (Yangsia 2017).
Produced as plates via a cold- or hot-rolling process, marine-grade steel offers the best durability and sturdiness in extreme temperatures and challenging weathers. These plates are usually used to manufacture ship hulls, bulkheads and other construction elements of various commercial vessels, including tankers, bulk carriers, container ships, etc. Although strong and durable, these steels have good weldability, which is desirable for manufacturing and repair processes.
Given the widespread availability of these materials, steel boat manufacturing and refit is a breeze for steel professionals like Bering. Welding equipment and specialists are available. To ensure integrity of the hull, welders should perform uniformed strength of the weld, and only certified high-quality specialists should be allowed to do so. WPQR, a welding procedure qualification record, is a hands-on test examining a welder's ability to perform complete penetration welding. Successful x-ray and resistance to rupture tests of the weld lead to a welder certification which is valid for two years. Such specialists are an exclusive commodity to the top shipbuilding companies.
As one of the most available materials, steel has a lot of advantages: durability, strength, weight (provides better stability). It is also cost-effective, relatively environment-friendly to work with and can be recycled to ensure a more sustainable process. (Yangsia, 2017) Admittedly, there are disadvantages if not constructed by an expert, including susceptibility to rust, which requires a special anti-rust painting, and weight, which tends to decrease speed. So, the manufacturers searching for lighter-weight materials, might also take a look at aluminum and/or fiberglass.
Aluminum
Aluminum is the most used nonferrous metal on the planet. Lightweight and silver in color, it is the most widespread metal that does not include iron on Earth. As a result, aluminum is popular in shipbuilding. It allows the creation of lightweight and fairly durable boats. Notably, however, this material is very costly (about five times higher than steel). Nevertheless, aluminum might be considered by some as an alternative to steel because of its weight and corrosion resistance. (Djukanovich, 2016).
The most popular aluminum alloys for use in corrosive environments such as seawater are the 5xxx and 6xxx series alloys, which demonstrate adequate strength and good corrosion resistance. The traditional and the most often used Al-alloys in shipbuilding are 5083 type Al-Mg alloy for plates and 6082 type Al-Mg-Si alloy for extrusions. These alloys are generally reliable in marine service as well as during manufacturing. (Ertug, 2015)
Considering manufacturing and refit, aluminum might be tricky to work with. Welding aluminum is very different from welding steel. Partially this is because there are fewer specialists who know how to properly weld aluminum, and also because the equipment is not that widely available. The material has to be cleaned and prepped for welding; the welder has to be aware of aluminum thickness to avoid burn-throughs, and because of its high sensitivity, the weld must be protected from air and dirt contamination. Tungsten inert gas (TIG) and metal inert gas (MIG) welding, two most popular methods of joining aluminum parts, as well as laser beam and electron beam welding, resistance welding, and shielded metal arc welding, all require complicated equipment.
As with all things, despite its benefits and utilities in naval construction, aluminum is not perfect. Light boats need expensive and energy-consuming stabilization systems for comfort. Additionally, aluminum is challenging and therefore expensive to repair. Furthermore, the price of aluminum is considerably higher than steel. And though resistant to corrosion, aluminum is quite susceptible to electrolysis. Ultimately, aluminum is a good reliable material for numerous applications that should be considered by boat builders who are looking for its specific benefits and prepared to overlook its shortcomings.
Fiberglass
Fiberglass is a composite material created from a plastic base and reinforced by glass fiber. Production of fiberglass uses different plastic materials such as epoxy, polyester resin, vinyl ester resin, and can employ a number of fiber layouts such as random arrangement, flattening into a sheet, or woven into a glass cloth. This material is light, reasonably durable, and non-corrosive. It is heavier than aluminum and lighter than steel. The chemical base for the fiberglass is silicone SiO2 with an addition of aluminum oxide, alkali oxide, calcium oxide, magnum oxide, boron oxide, and other composite materials to create a large number of combinations and proportions. Many types of fiberglass are produced to fit different tasks.Importantly, however, one of fiberglass's biggest shortcomings is its susceptibility to mechanical stress.
Significantly, there is no "marine-grade fiberglass." One of the most widely used types of glass fiber in naval construction is E-glass, which is aluminum-borosilicate glass with less than 1% w/w alkali oxide. Pultrusion, the process of manufacturing fiberglass, has silica (glass) heated until molten, then it gets forced through superfine holes thus creating extremely thin glass filaments. These filaments get woven together into different patterns, and then various resins are added to the woven mat. During the process, fiberglass parts can be molded into desired shapes or forms.
With hundreds of applications and the high plasticity of the material, fiberglass creates relatively lightweight and durable boats. Though it responds well to the outside environment, when damaged, fiberglass is not easy to fix. The owner has to have a certificate/description of the composite material used to build the boat in order to choose the right one for repairs. It might be difficult to find the correct type of fiberglass, and, unfortunately, few repair shops have knowledgeable staff or equipment to properly fix composite boats.
Fiberglass certainly has advantages such as sturdiness, plasticity, and resistance to elements. But it is easier to mechanically damage than aluminum and steel; the material costs more than other two, and there are questions about harmful emissions of fiberglass. However, its advantages make it an important consideration for marine construction.
Fiberglass vessel acceptance
One of the steps of inspecting the fiberglass boat before the launch is cutting out a piece at any location in the hull. This cutout is measured and inspected and then the hole is repaired. This process is intended to ensure the integrity and quality of the boat-building materials.
Boat function defines the materials that are used to build it. As a general rule, a pretty and speedy boat will be made from fiberglass. Fairly sturdy and speedy - from aluminum. A displacement boat, a slow but sure moving house or even a fortress on the water capable of going to any point of the globe no matter the conditions, will be made of steel.
The goals and expectations of every type of recreational boat are quite different. However, there is one issue that has to be considered first, no matter the boat type: SAFETY. How safe is your boat? How resistant is she to impact, fires, and the extreme elements? At Bering Yachts, we believe that answering these questions leads to a single conclusion: despite the relative benefits of aluminum and fiberglass, steel is in a class of its own.
This is chapter one of Bering: Made of Steel article. Follow the updates for the release of the next chapters.
To learn more about Bering: Made of Steel, please watch our Bering Exclusive video on YouTube and subscribe to our Instagram.