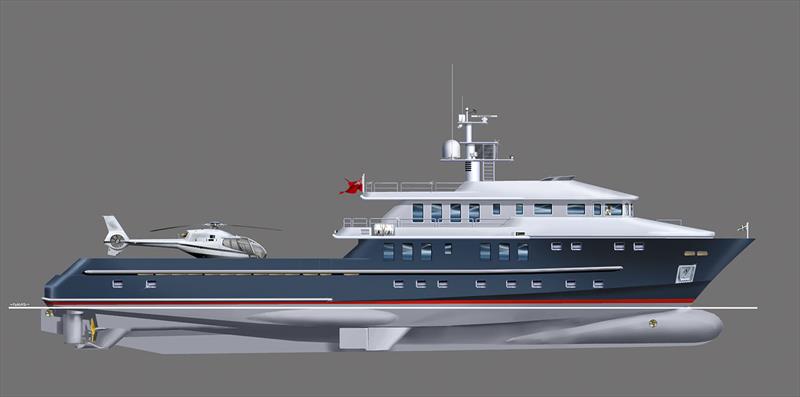
42m Explorer Yacht with helo - photo © Bray Yacht Design
Dear Recipient Name
Throughout the course of the journey, we have been privileged to have great intel from Naval Architect Pat Bray. Resident of British Columbia, Bray has brought to the table brilliant insight into passage making for large vessels. This pertains a lot to what we now call the fast displacement hull form, where craft do most of their work at say 8-10 knots, and perhaps up to 12, but have a sprint speed of less than 24 knots.
We first looked at the bulbous bow in It ain't necessarily so, and then subsequently the hull form, and very much including hull manufacture in Square peg, round hole. Round peg, square hole.
Now, after an epic 16-year project looking into it all, we can show what the combination of bulbs on the bow, midships, and stern not only look like, but what they deliver in the real world. This is significant, for it arrives into a world where fossil fuel prices are eye watering, and a time when the change of pace afforded by boating is so keenly sought.
Yes, the kerosene canary gets you there super-pronto. The go-fast boat sounds wicked, as does a turbine-powered cat. The centre console has bragging rights with an in-your-face rack along the transom, and the dash to back it all up. The Italian hoonwagon lives on with incredibly sophisticated high speed Diesels, waterjets or surface drives making fifty knots seem like everyone should be doing it. So, we are not talking about the death of the planing hull form, at all. In fact, interesting developments abound [see video].
However, being slippery, efficient, and miserly is well and truly the new black. It also affords a very different social conscience. Very.
Lay it on me, brother
Now to set all of this up we need to state that all of this work has been carried out on a 45m platform, to give a universal, and level playing field. Possibly even more crucially, there is a cascading set of cause-and-effect elements that very much need to be spelled out.
So. If you are far more efficient, you are going to need less horsepower to push the vessel through the water. Water is dense. It does not like to compress. Just ask anyone who has taken their car through a puddle way deeper than their wading limit. A hydrolocked motor ceases to function very smartly, and leads straight to bent conrods, piston damage, dropped vales, and all manner of very, very expensive repairs. So if you carve your way through with a scalpel as it were, then it is way better than trying to bludgeon your way across the seas in something akin to a mallet.
Less horsepower weighs less. A lot less, actually. However, you still get the same speeds. It burns less. Much less as it turns out, and that means less bunkering required for the same distance, or more nautical miles should you opt to carry the same volume of fuel. With Explorer vessels becoming very de rigueur, that point is very self-explanatory. No bowsers in the high latitudes...
The powerplants are also physically much smaller, and of significantly lower overall mass. Potentially, they are also quieter, too. Upshot? Less space handed over to the engine room, which then goes straight back into the accommodations. It also means ancillary gear, like ventilation, is also smaller again, drawing less power, and more than likely meaning smaller gensets need to be installed. Quite a few ticks in that lot, to be sure.
Not all new, but very much now
The stern bulb goes back to Japanese commercial shipping in the early 70s, and the Canadians adopted the bulbous bow for their fishing fleets as fuel prices took off not that much later. Today we have things like concave sections [video], and the transom or hull vane [video] that is a lot like a diffuser under the bumper of a fast and expensive car. They are all great, and do many good things, but it is fair to say that the paradigm has moved on.
Let's begin the journey of unwrapping it all, then.
The study was all about seaworthiness and efficiency over a wide range of displacement and high semi-displacement speeds. As Bray says, "The initial concept was for a long-range vessel capable of serious ocean passages at displacement speed, with a comfortable motion, good stability characteristics, and with very good fuel economy. It was all about covering long distances to various cruising grounds, where the vessel could then power around at higher semi-displacement speeds, whilst still maintaining the same high degree of comfort and fuel efficiency, and then return home again in displacement mode. This extended range could also be used to add considerable 'loitering time' at any location, reducing the need for fuel stops."
"We looked at the addition of various appendages to reduce resistance and/or improve seakeeping, and these came in the form of a bow bulb, midship bulbs, and stern bulb. Having reduced the bow wave with a fine entrance angle, and the use of a bow bulb, attention was turned to reducing the midship hollow. The goal was to help reduce drag by reducing the overall wave train, and increase stability under way by reducing the midship hollow: essentially, to duplicate the success of the bow bulb with a midship hydro-fairing."
"This is done by creating a high-pressure field in the middle of the midship hollow, which is traditionally a low-pressure area. The success of this is evident by the graphic presentation of the wave profile that through the wave height above static waterline, shows the hydrodynamic pressure produced by the passage of the hull. The midship hollow is reduced a small amount, but enough to have a very positive impact on the overall vessel resistance. A maximum resistance reduction of 6% has been noted," stated Bray.
"Of course, size and placement are critical to produce the desired impact within the desired speed range. With the reduction of the bow wave and midship hollow, the final task came down to reducing the stern wave. The stern end bulb (SEB) was developed in Japan in the late 70s with good results. At that time, fuel prices were comparatively low and the development garnered very little attention. With current increases in fuel costs and more attention being paid to carbon fuel use, it seemed time to resurrect the stern bulb, and then investigate if there was any synergy with our other appendages."
"The stern bulb's impact on the wave train is again subtle, but still a reduction in overall resistance of 7% was achieved in the Japanese tests. This appendage reshapes the stern wave, and also lowers its profile. Assuming a potential for a compounding effect of all the appendages, reducing the resistance while providing additional displacement, then the benefit would be even more than first observed."
Not always possible without the thanks
So. This all stems from three studies that include firstly towed models, and then Computational Fluid Dynamics (CFD), which have increased in performance directly in line with computing power. The third and most recent project involves a far more extensive CFD series, utilising the National Research Council of Canada's Ocean, Coastal and River Engineering Research Centre's expertise in numerical modelling. The project also received support in the form of advisory services and research and development funding from the NRC Industrial Research Assistance Program (NRC IRAP).
"The resistance reduction focused on constructive/destructive wave interference and by reduction of the running trim due to the hydrodynamic forces acting on the various bulbs. The appendages modify the hull waves through their own small wave and pressure patterns, and it is this interaction that reduces the overall wave train, resulting in a reduction to the overall resistance," said Bray.
"Existing vessels do benefit from retrofitting these appendages but there is an increase in displacement (and Gross Tonnage) due to the volume of the forms. The real advantages are in new construction as the reduction in powering and fuel consumption while still achieving all performance goals then allows for further reduction in vessel weight. This is then achieved by reducing the volume of the main body of the hull, lowering resistance, resulting in a spiral of benefits."
All of these factors impact the resistance, and thereby the powering, making the resistance advantages even greater than it first appears. In this example, the un-appendaged (bare hull) version has 745,253 lbs of hull volume versus the final appendaged version's 802,756 lbs, which is an 8% increase in displacement.
Now, at the same time this heavier, more efficient final version has up to 116% greater range for the same fuel bunkering (10,000 US Gallons). Mostly, this is due to the un-appendaged version having 23-26% more resistance over the 12-20 knot speed range.
And here's the heading
So you're thinking: one percentage increase in range. Whoop de do! Right? Take another look.
At 20 knots there is a reduction of 1000 shaft horsepower required. That's going to be easily something like two metric tonnes of extra iron mass you do not have to house on board (both displacement and physical dimensions), firstly carry and then feed precious Diesel to, and then at the lower displacement speeds, lug around for the day when you do need to light the wicks. That's way more than one percent, right there!
So, at 12 knots the bare hull needed 568hp, burned 26.2GPH, and had a 4573 nautical mile range (NB, this is without genset run time). Whereas the fully appendaged hull needed 21% less hp at 450 ponies, burned just 20.8GPH, and delivered a 5772nm range. This too is without the genset to keep it all even.
Right then. At 20 knots the bare hull needed 5686hp from two CAT 3516E Diesels delivering 2843hp each, weighing a hefty 21,164 lbs each (dry BTW), and burning a massive 270.2GPH to deliver a 740nm range with no genset running.
OK. Now the fully appendaged hull needed just 4625 hp from its two CAT 3512C Diesels delivering 2312hp each, this time only weighing 16,508 lbs each (dry), and chewing just 219.8 GPH for a 910nm range, again without any genset calculated in.
Stack it up and it looks like this:
- 19% less horsepower, and all the benefits associated with that.
- 4,656 lbs savings in mass, per side, for a combined reduction of an incredible 9,312 lbs.
- 750 gallons less fuel burned to achieve the same range, which is a further saving of 5,400 lbs.
- This means the total saving is a staggering 14,712 lbs or 6,673kg!
Bray added, "This does not take into account any reduction in hull plating or interior cabinetry, but all of it does impact the overall powering and fuel consumption. Therefore, a fully appendaged version with equivalent performance (taking into account these additional reductions) would inevitably result in an overall lighter vessel. Again, this gives an ever-improving spiral of benefits.
"The spiral of benefits looks like this. At this size of vessel and weight, it takes 1hp to move every 158 lbs of completed vessel. By being more efficient, it takes less power to move, which burns less fuel to achieve range, which means less weight, which means less hp, and so on, and so on."
"This increase in efficiency is evident in the wave train of the bare hull (top images) as compared to the full appendaged hull (bottom image). The bare hull images are from the 2016 test program, and the software imaging was not as refined as the 2022 imaging, which shows far greater detail. Still the overall wave pattern is very discernible.
"The primary waves to notice are the midship waves and the stern waves especially at 20 knots."
The bow's not the only thing with a point
"Lowering the environmental impact of a vessel isn't just about the propulsion system, it starts with the power required to move the hull. We feel there are numerous ship applications for these appendages, in reducing both consumption of fossil fuels, and the impact of vessel wake on shorelines, as well as reducing the quantities of raw materials required to construct these more efficient and therefore lighter weight vessels.
"These benefits would apply in both pleasure craft and commercial vessels, with applications for fast ferries, Coast Guard vessels, research ships, patrol, and of course, yachts."
"Various aspects of this technology have been incorporated into our vessels for years. It is completely scalable so it can be used on a wide variety of sized vessels. It is ocean tested, and owner approved. A new line of long-range vessels is in the works that will take advantage of all of these features. In addition, a prominent North American marine group is considering this technology for their new 45m patrol vessels," said Bray in closing.
OK. Today you will find that the website has an abundance of material from right across the globe, and if you cannot find something, just try the search button right up the top of the landing page, above our logo. If you cannot find what you want or wish to want to add to that, then please make contact with us via email.
Finally: please look after yourselves,
John Curnow
Global Editor, Powerboat.World
|