Arksen 85/02 Project Pelagos sold
by Arksen 30 Sep 2021 04:20 PDT
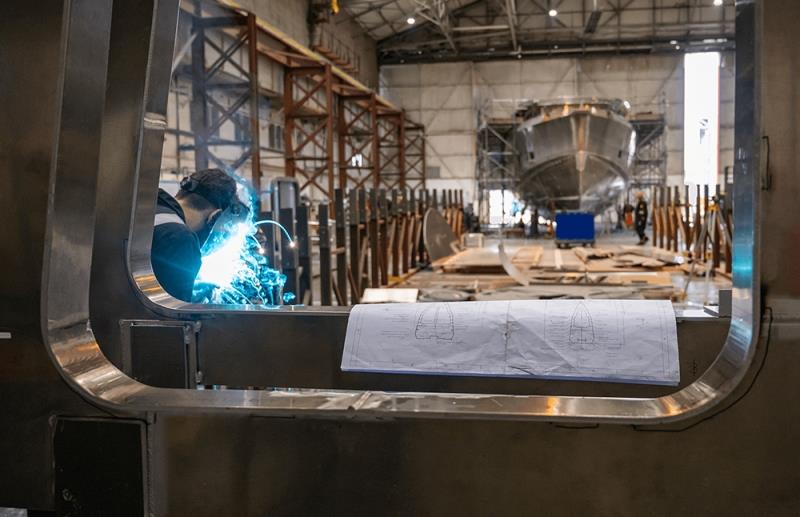
Arksen 85 - first weld © Arksen
Two and a half years ago, Arksen unveiled its vision for a new concept in sustainable marine adventures. The ambitious project has rapidly gained momentum with the sale of the second Arksen 85, Project Pelagos, announced today.
The Arksen 85 represents the 'flagship' vessel within the Arksen Explorer Series, with the Arksen 75 and Arksen 65 making up the 'Explorer' fleet.
Currently in build with Arksen's build partners Wight Shipyard in Cowes, on the Isle of Wight, Project Pelagos is due to be on the water by November 2022, providing 12 berths in a six-cabin configuration. As with all Arksen vessels, the Arksen 85 offers robust build quality, excellent reliability and superb efficiency, combined with comfort, style and safety, as expected from a modern, long-range cruising vessel.
The Arksen 85
The Arksen 85 is designed to access remote areas of the globe and operates safely in extreme environments whilst being equally capable of cruising in more accessible waters. The design of the vessel and the on board systems allow for operation in a wide range of conditions, including high latitudes, tropical climates and adverse weather as well as extended periods in remote regions without external support.
Through the purchase of Project Pelagos, the new owner will join the Arksen family, a growing and supportive ecosystem that helps owners discover more remote and challenging locations, giving them the tools and confidence to undertake voyages with friends and family.
Arksen Head of Sales, John Solomon, said: "I recall my very first conversation with the new owner of Project Pelagos. As he described the key criteria for his family's next vessel and the adventures that they wished to undertake, it quickly became clear to both he and I that the Arksen 85 was an ideal fit. He wanted to achieve trans-ocean cruising, high efficiency, the ability to explore high and low latitudes, easy operation, and low maintenance while having the latest proven and reliable technology.
"Central to the final decision was Arksen's ability to personalise the vessel, and so we made significant customisations, including changes to the cabin layout and interior finish."
John Solomon, Sales Director, said: "We work closely with our clients, designers and systems engineers to create a personalised solution that results in something truly bespoke."
Interior design
The interior is designed in line with Arksen's core values of functionality, beauty and sustainability and offers a calming ambience throughout, focusing on light and airy spaces. An environmental approach was at the heart of the design process. The materials have been selected to enhance the experience onboard, while minimising damage to the environment where possible.
"We didn't want to be just another boatbuilder, we want to provide our owners with the opportunity for life-enhancing experiences to help foster a greater connection between humanity and the ocean. With a more sustainable approach in design, construction and operation of our vessels, we strive to be part of the important transition within the marine industry and hope to get the third hull of the Arksen 85 under way at the end of this year." - Jasper Smith, Arksen's Chairman.
The third vessel
Arksen 85 hull number 3 is scheduled to start construction in late 2021 with delivery available in Summer 2023. For more information on this or any other news from Arksen please get in touch.
Hull turning - why?
We recently turned the hull of the first Arksen 85 (Project Ocean) representing a major milestone in the build process. But what does 'turning' a vessel mean and why was this project started upside down? We sat down with Jim Mair, Arksen Technical Director, to reveal all.
Why are some boats built upside down and why did we choose to build the Arksen 85 in this way?
Jim Mair (JM): Not all aluminium vessels are built upside down. However, the reason we chose to build the first Arksen 85 like this is because of the shape of the hull.
If you imagine the deck of a boat, the area that you stand on is more or less a flat surface. The lower portion of the hull is obviously quite a curved and complex shape, but if you turn it upside down you've got an almost flat surface that you can build everything up from. Boats that have to be built the right way up, for other reasons, can lead to some complicated support jigs to make sure that everything is held upright, level and in the correct position during the construction process.
The second reason is due to access. The build team need to be able to get into relatively small spaces, fabricate the boat, weld and complete the construction of the hull. When you're welding, it's easier and faster if you can weld in a downwards or across direction. As soon as you try to weld upwards or above your head, it gets more difficult, takes longer and there are more processes you have to go through to make sure that everything is done to the right quality and safety standards.
So by building upside down, we can accomplish much more of the easier welding before the point at which the boat is turned. This is beneficial in terms of the speed and efficiency at which the build can progress.
So it's more beneficial?
JM: Yes, definitely. There are many good reasons to start a build upside down if all the factors that go into making that decision are aligned.
The other point is that much of the outer surface shell plating is made up of large heavy sheets of metal that have been formed into specific shapes with different curves. It's easier to move this shell plating down onto the structure below and use gravity to hold it in place whilst welding.
With the boat the right way up, you're doing exactly the opposite, working against gravity trying to manoeuvre and hold these big pieces of metal in position.
Are there any challenges of building upside down at all?
JM: The vessel design has to be thoroughly planned and understood before you even start building it. Otherwise, you can get into real trouble.
There comes a point when more complicated systems and fitting need to be integrated into the build and working with the boat upside down can prove to be more difficult as you have to continuously flip the design in your mind. For instance, if something needs attaching to the floor of the boat, that would currently be the ceiling. But everything has been designed for this way of building so there are no challenges that we've come across so far.
Who turns over the hull?
JM: The shipyard that we are using to build the Arksen 85, Wight Shipyard Co. are responsible for the hull turn. You can see in the video that the shipyard has large overhead cranes they first use to lift the boat evenly, then lower one side so it starts to rotate until it is held half way through the turn. Whilst held in this position, two further mobile cranes are attached to the lower side which support the vessel as it continues to slowly roll upright. It is well choreographed, and although quite nerve-wracking, it is always an exciting moment!
The team at Wight Shipyard Co. did a great job. The whole process was completed quickly and smoothly. There's a lot of planning required for moving something of this size and weight with the potential risks involved.
Why is the turning of the hull such a significant milestone in the build?
JM: The main reason is that it's such a visual event. For those involved in a project, this is a great moment because it suddenly starts looking like a real boat.
As soon as the hull is the right way up, it opens the doors to other work that can be completed and it all starts coming to life more quickly. You have this short phase at the beginning, where you see the build go from nothing to all of a sudden there's this recognisable object coming together.
So how far through the build of Project Ocean are we?
JM: I would say we are at about 25%. When the boat is upside down, just the aluminium work is carried out, so now we've turned it over we've got everything else that goes inside; pipework, electrical work, furniture etc.
What are the next stages of the build?
JM: Welding the superstructure living areas above main deck level is the next phase of work and finishing all other 'hot work'. Once these are completed we will be able to start fitting other materials to the boat.
And what about the next milestone in the build?
JM: Building the interior will be the next milestone for us. We start by mocking up certain areas of the interior in 'real scale' before building and installing the finished units.
How long will the rest of the build take? When are you expecting the final delivery?
JM: We're looking at an early 2022 delivery date!
Weight control is often talked about in yacht design and during the build. Why is it important?
JM: When a boat is designed, it is calculated to be a certain weight. This is so it sits in the water at the right level and angle without leaning in any direction.
The stability, comfort and safety of the boat all stem from the weight and also the centre of gravity. If you have too much weight higher than the point at which it's supposed to be, that's not good news, because the boat becomes less stable. But if the weight is lower than expected, that's potentially better.
In addition, it can impact the way the boat behaves when it's under way. If the boat is the right weight and it's balanced properly, you'll achieve maximum efficiency in the water. If the boat is sitting back slightly, it can become inefficient.
It's very important to control this, so we constantly monitor the Arksen build to ensure the projected weight is maintained at each stage.
How much did the boat weigh at the point of turning the hull?
JM: At the point of turning the hull, it weighed approximately 13 tonnes. Once completed, she'll be 70 tonnes.
What's been your favourite part of the build so far and what stage are you next most looking forward to?
JM: My favourite part of it so far is probably the point at which we got all of the hull plating on, the shell of the boat, because that's the stage at which it really starts taking shape. You can then see the effect of all the careful design work that's gone into designing the hull, the curves and the overall shape.
However, that will probably be replaced by the point at which we finish building the superstructure because that's when you can stand back and it'll be really recognisable as an Arksen. We've spent a lot of time looking at the renderings and the drawings, but that will be the point where you can stand back and it'll finally be visible.